Hauts fourneaux
Hauts fourneaux
Construction : de 1883 à 1916,
ensuite, le chemisage des hauts fourneaux avec des briques réfractaires fut rénové tous les 10 - 15 ans.
Durée d'activité : 103 ans jusqu'à l'arrêt
Les conduites de gaz des hauts fourneaux soulignent la silhouette de la fonderie. Elles récupèrent le gaz des six hauts fourneaux. Les hauts fourneaux mêmes (le premier date de 1883) sont à peine visibles, cachés derrière des échafaudages, des conduites, les cowpers et les cheminées.
Toutes les 2,5 à 3 heures, 130 t de fonte brute en moyenne étaient déversées, près de 1 100 t par jour et par haut fourneau. Les hauts fourneaux étaient chacun dotés de trois cowpers. Ils chauffaient le vent des soufflantes à 1 200°C. Dans la partie inférieure du haut fourneau, les températures atteignaient 2 200°C.
Le monte-charge incliné
Les matières premières étaient déversées dans les six hauts fourneaux par un système de voies ferrées unique. Le skip électrique a été installé entre 1911 et 1918. Le système de voies s'étendait sur près de 6 kilomètres. Elle permettait d'alimenter les hauts fourneaux avec une moyenne de 310 wagons suspendus. Leur bruit grinçant résonnait jour et nuit dans Völklingen. Cette construction empêchait toutefois l'agrandissement des hauts fourneaux. Le monte-charge incliné était conçu pour une hauteur d'exactement 27 mètres. La production de l'usine sidérurgique de Völklingen ne pouvait pas suivre l'essor de l'industrie métallurgique.
A l'arrière de la batterie de hauts-fourneaux, un ascenseur incliné du même type transportait le coke produit dans la cokerie jusqu'au niveau de déchargement, appelé plate-forme de gueulard.
Les appareils Cowper
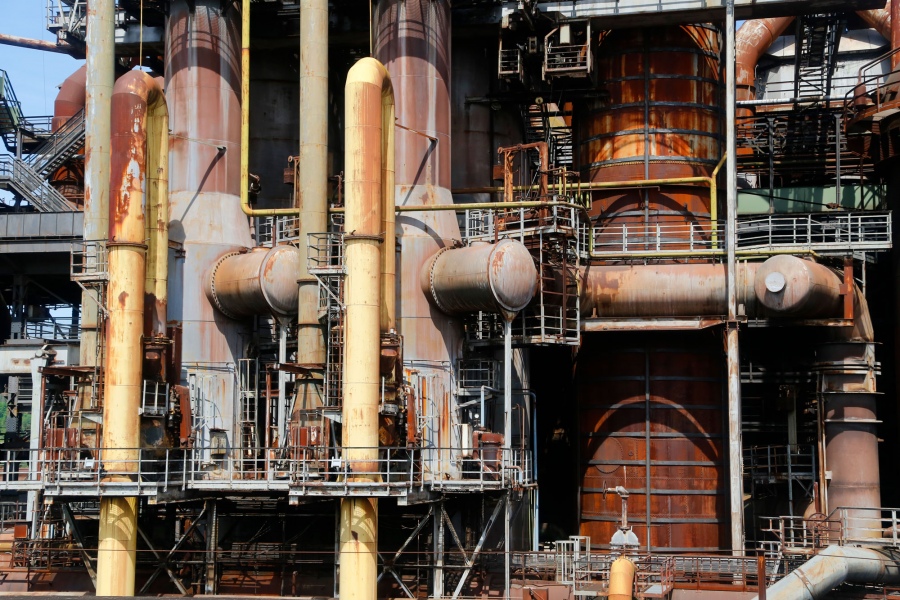
Vue détaillée du récupérateur d'air du haut-fourneau six
Copyright: Weltkulturerbe Völklinger Hütte | Karl Heinrich Veith
Les appareils Cowper de l'usine sidérurgique de Völklingen atteignent jusqu'à 40 mètres de hauteur. Avec un diamètre parfois de près de 7 mètres, ils constituent à côté des hauts-fourneaux les constructions les plus imposantes de la section hauts-fourneaux de l'usine. Les briques se trouvant à l'intérieur des appareils Cowper étaient chauffées au gaz. Lorsque celles-ci étaient suffisamment chaudes, le vent froid des soufflantes était insufflé aux appareils Cowpers. Ce procédé permettait de porter le vent chaud insufflé aux hauts-fourneaux à des températures de près de 1200°C. Sur le Cowper 6.3, l'appareil générateur de vent chaud pour le haut-fourneau 6, l'inscription allemande pour « vent froid » est encore clairement lisible.
La plate-forme de gueulard
La plate-forme de gueulard relie les six hauts fourneaux à un seul niveau. C'est sur ce niveau que sont guidés les wagons de la voie suspendue. La plate-forme de gueulard est longue d'environ 240 mètres et s'étend à une hauteur d'exactement 27 mètres. La plate-forme de gueulard tire son nom du mot "Begichten", qui désigne le remplissage des hauts fourneaux avec les matières premières nécessaires à la production de fer. Le minerai de fer, l'aggloméré, les additifs, le coke, mais aussi les résidus ferreux de l'industrie ou la ferraille étaient déversés dans la gueulard, la trémie de remplissage du haut fourneau. La "hotte", la fermeture supérieure du haut fourneau, était soulevée, puis cinq wagons suspendus étaient déplacés autour de la trémie. Sous la hotte se trouve une deuxième fermeture, la "cloche". Elle restait fermée pour recueillir les gaz de gueulard. Le matériau était basculé sur la cloche, puis la hotte était abaissée. Ce n'est que lorsque le capot était fermé que la cloche était descendue : Le matériau glissait dans le puits du haut fourneau.
Hauts fourneaux
Les six hauts fourneaux de la Völklinger Hütte font tous 27 mètres de haut pour un diamètre extérieur de près de 10 mètres. Ils ont été construits entre 1888 et 1916. Ils ont toutefois été plusieurs fois rénovés, transformés et agrandis.
Les hauts fourneaux dans leur forme actuelle datent des années 1870. Les hauts fourneaux de la Völklinger Hütte avaient une capacité de plus de 1 000 m³. Les hauts fourneaux de Völklingen sont entourés d'un revêtement de tôle d'acier de 3 cm d'épaisseur. L'intérieur est composé de briques réfractaires. Dans sa partie supérieure, le chemisage des hauts fourneaux mesure 60 cm d'épaisseur. Dans la partie inférieure où les températures sont plus élevées, le chemisage mesure 1 m d'épaisseur.
Pourtant, cette maçonnerie imposante ne suffisait pas à juguler la chaleur intense à l'intérieur du haut fourneau : on faisait alors ruisseler continuellement de l'eau le long des parois externes pour refroidir le revêtement.
La coulée de fonte
Toutes les deux heures, deux heures et demie, le fondeur perce le haut fourneau. Deux trous de coulée sont percés dans le revêtement en acier pour extraire la fonte et le laitier. Les trous sont colmatés avec une masse argileuse que le fondeur peut percer et reboucher. Autrefois, les fondeurs ouvraient le trou de coulée du haut fourneau avec une perceuse manuelle pneumatique et une lance thermique. Plus tard, ils utilisaient une perceuse télécommandée. 130 tonnes de fonte brute liquide coulaient dans la rigole de coulée avant d'être versées dans les wagons-torpilles qui transportaient le fer vers l'aciérie. Lorsqu'elle sort du trou de coulée, la fonte brute atteint des températures supérieures à 1 400°C. Pour les six hauts fourneaux réunis, on parvient à un rendement journalier d'environ 6 000 tonnes de fonte brute. Les hauts fourneaux actuels peuvent produire plus de 10 000 tonnes de fonte brute en 24 heures, beaucoup plus que les six hauts fourneaux de Völklingen.